Open Source Air-Bearing Simulation
The analytical and numerical simulation of air bearings has been a field of research for a long time. As such, the history and various methods and approaches are well documented in the literature [1]. However, their implementation requires considerable knowledge of numerical mathematics and coding. Another option is multi- physics software such as COMSOL. It is being used for air-bearing simulation [2] [3]. We found that quite some modeling effort is necessary to achieve good results. Especially for micro-groove and restrictor-regulated bearings and subsequent model fitting, customization is required. While certainly an option to consider for many applications, there are drawbacks to using a small part of a large software suite to analyze a narrowly defined problem. One example is the licensing cost. Combined, there might be a barrier to entry for some and a significant time investment for others to simulate an air bearing. It could be speculated, that considerable duplicative effort has been made to model or write what is essentially the same software, by researchers the world over. The air bearing simulation described here does not claim to be novel in the modeling approach, but rather in the fact that it is an open-source project with accessibility and modularity in mind. Eitzenberger will release the first version of the simulation on Github by the end of 2024, hoping that others will find it helpful, and will consider joining the collaborative development.
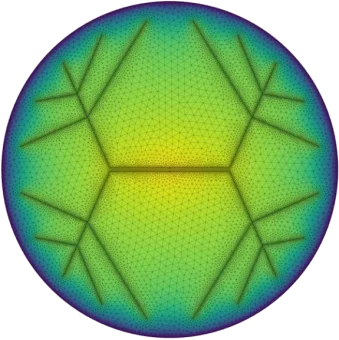
Pressure distribution of an Eitzenberger nozzle and micro-groove regulated air bearing at a given air gap.
Driving Simulator
The driving simulator, a cabin with all-round projection and an integrated car, is mounted upright on a hexapod and a linear axis. For a driving simulation that is as realistic as possible, the hexapod is moved linearly on the air-bearing axle. EIZENBERGER developed and built the air bearings for the linear axis and carried out the fine machining of the rails on site. A particular challenge was the combination of high resilience and rigidity, a large operating air gap and the desire for a design that was as compact as possible with a low mass. The air bearings are operated at 9 bar. The driving simulator accelerates at up to 10 m/s2.
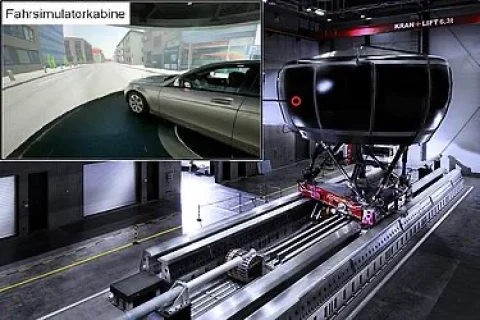
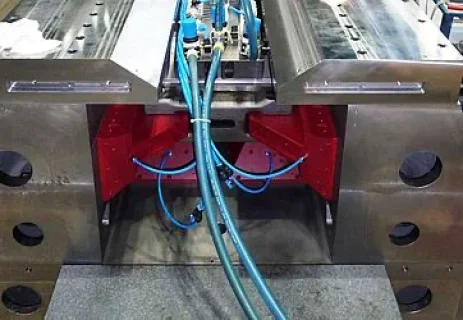
7-Axis System
Rolling Road und Conveyor
These systems are used in the automotive sector in so-called environmental wind tunnels (EWT). With the EWTs, the road is simulated by a three meter wide endless steel strip on which the car stands. The belt is pulled under the vehicle at a speed of up to 300 km/h. The Rolling Road wheel support bearings are located under the treadmill. They consist of high-pressure air bearings, which are supplied with 24 bar to support the tire contact area. They are supplemented by air bearing-vacuum combinations that guide the steel strip independently of the positive or negative pressure acting under the vehicle.
Polygon-Scanner
The air-bearing scanner axis is designed for a speed of up to 60,000 rpm. The axis is wear-free due to the air bearing. Cylindricity error of the polygon facets is < 1 µm.
Fast-Tool
The air-bearing Fast Tool is used for free-form turning of plastic lenses and is suitable for use in wet machining environments.
High-Speed Linear Axis
High-speed axis with air bearings, stroke 600 mm; velocity 8 m/s. acceleration 180 m/s2, repeatability 0.2 μm. The axis is suitable for fast and precise pick-and-place applications in the semiconductor industry.